Electric mobility and autonomous driving are the big trends in the automotive industry. This means that parts and components as well as manufacturing processes are changing and there will be new and different tasks for parts cleaning, writes Doris Schulz.
The change in mobility is not only leading to new and changed requirements in the automotive and supplier industry, but it is also having an impact on industrial parts cleaning. In addition to particulate contamination, filmic-chemical contamination due to the surface requirements of such downstream processes as bonding, welding and sealing play a greater role. What’s more, greater focus is being placed on the technical cleanliness of production and assembly lines as well as production equipment in order to eliminate recontamination and cross-contamination.
Cleanliness-relevant systems in the electric vehicle

Whether power electronics, battery technology or thermal management – in order to avoid recontamination and cross-contamination, a highly clean production including production equipment and environment is indispensable for many tasks. Image source: LPW Reinigungssysteme
An electric motor, an energy system in the form of a traction battery or fuel cell, and power electronics are the three essential components that distinguish an electric vehicle from one with an internal combustion engine. There are specific cleanliness challenges with each of these systems.
In the case of the electric motor, for example, the first concern is the technically clean production of each individual component, such as the stator, the rotor and the housing. Cleaning technology offers the corresponding, for the most part wet-chemical solutions for these tasks, with which even extremely demanding particulate cleanliness specifications can be met. However, cleanliness problems often arise during the final assembly of stators, for example, in the form of metallic and non-metallic particles from pre-processes. Dry cleaning solutions are required for their removal, which can be easily integrated into the assembly line – even retroactively if required – and enable effective, automated individual part cleaning in the production cycle. One aspect that should also be taken into consideration is the cleanliness of such production equipment as handling systems and grippers in order to prevent recontamination.
Parts2clean – Leading international fair for industrial parts and surface cleaning
What methods can be used to make the cleaning of different components process-safe and economical? What technologies are available for dry and partial component cleaning? How can cleaning processes be efficiently integrated into fully automated manufacturing environments? How can the cleanliness achieved be validated and documented? parts2clean offers answers to these and many other questions about industrial parts cleaning. The leading international fair for industrial parts and surface cleaning is scheduled to take place on the Stuttgart Exhibition Grounds (Germany) from September 26 –28, 2023. The fair will provide comprehensive information on cleaning systems, processes and media, quality assurance and testing procedures, cleaning and transport containers, disposal and reprocessing of process media, handling and automation, service, consulting, research and technical literature. The three-day technical forum at parts2clean will also provide a great deal of cleaning know-how. www.parts2clean.de/en.
Clean manufacturing for energy systems
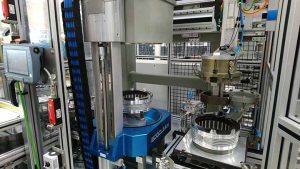
Dry cleaning solutions, such as this compressed air cleaning, are used to remove impurities from pre- processes such as metallic and non-metallic particles during the final assembly of stators, for example. Image source: Ecocean/ZF
The traction battery in the form of lithium-ion batteries is the preferred energy system in electric vehicles today, accounting for a decisive share of added value. Cleaning steps can be integrated into the series production of the batteries before or after various manufacturing steps. This begins in the production of the electrodes with the cleaning of the substrate before coating, continues with the cleaning of the electrode sheets after separation by punching or laser cutting, and ends in battery pack assembly with the preparation of the adhesive surfaces of the battery pack cover after the modules have been integrated. The interconnection of the cells by electrically connecting the contact surfaces with the arrester, e.g. by ultrasonic bonding, is considered to be a safety-relevant process in battery module production. Joint areas contaminated with particles and filmic residues can lead to insufficient contact, resulting in very high contact resistance values and overheating as a consequence. When assembling battery cells into battery packs and integrating them into the battery tray, particles with a size of several hundred micrometers are considered critical.
The manufacture of fuel cells also places high cleanliness requirements on processes, production equipment and the environment. Its central component, the bipolar plate, consists of an anode and a cathode made of thin stainless-steel sheets, among other materials. The production steps are forming, cutting, joining and coating. Since the starting material may be contaminated and residues from machining remain from the first three processes, several cleaning steps may also be required here. This is because particles just a few tens of micrometers thick can cause leaks.
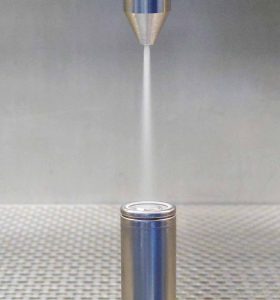
Clean contact points are crucial in the electrical connection of the battery cells for high energy density and the safe functioning of the battery. CO2 snow blasting technology, which can be integrated into the bonding process, is ideal for cleaning. Image source: acp systems
Power electronics – a case for the clean room
The power electronics are located in a housing between the battery and the electric motor and are in effect the control center of the electric vehicle. The component called inverter converts the direct current from the battery into alternating current as required by the electric motor. The electronic assemblies installed in power electronics, such as semiconductors and electromechanical components, place extremely demanding cleanliness requirements on the production and assembly environment. Due to the high voltages and currents occurring during operation and the resulting power, not only metallic particles can become a problem here, but also fibers, which become critical due to the absorption of moisture. In this case, a clean room is required for many applications.
Complex thermal management is also required in electric vehicles. It is responsible for cooling the battery, motor and power electronics at different temperature levels as well as for air conditioning the interior. High cleanliness requirements must also be met when cleaning the components for this sophisticated management of the heat flows generated in the electric vehicle.
Cleanliness – a functionally relevant characteristic for sensory components
Whether for surveillance tasks or assistance systems or autonomous driving – the demand for such high-quality optical and optoelectronic systems as camera-based sensors is growing. Whether these systems can function without errors under all conditions and temperatures decisively depends on the particulate and filmic cleanliness of the optics and electronic components, as well as the housing parts. In this case, particles as small as a few micrometers and the finest filmic layers, as well as outgassing from components, can lead to the attenuation of signals and incorrect information.
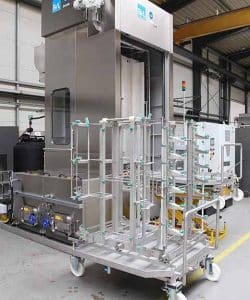
For cleaning in the turntable system, car body parts up to 2,200 mm long, e.g. extruded profiles, are fixed vertically and positioned precisely on the areas to be cleaned. Image source: BvL Oberflächentechnik
More lightweight structural components for more range
Range is a key criterion for electric cars, so the weight of structural components is highly relevant. On the other hand, it also requires the chassis to be highly rigid and strong. This results in the increased use of lightweight materials such as aluminum and hybrid materials. At the same time, joining technologies are also changing – there is more bonding and welding. The surfaces must be prepared for these joining processes in an optimally coordinated way. Depending on the material and joining process, this may also involve the removal of filmic contaminants that have been incorporated into the surface by machining and forming. The selection of the right cleaning process – wet chemical, possibly combined with an increase in surface roughness, or a partial treatment of the joints directly before or integrated into the joining process – has a significant influence on the quality of the joint.
Electric mobility is also creating new and changed tasks for OEMs and suppliers in the field of component cleaning. To come to an optimal and economical solution, the cleaning task should not be considered in isolation, but rather looked at in the entire production chain, along with the cleanliness of the production equipment and the environment. This often requires a process-oriented rethink. ACI
Also read, Reviewing Product Life Cycles