T Murrali
With rising competition coupled with ever increasing operating cost the challenge for
any component manufacturer to stay afloat is to contain the cost of manufacturing.
This is gaining significance since these issues directly hit the bottom line and may
even pave the way for organisations to exit the business. However, options to contain
variable costs are falling due to inflation, slowdown, ever increasing diesel prices
coupled with power cuts. Therefore, the one aspect to contain operating cost is by
minimising the consumption of various resources including electricity and by resorting
to sources that are renewable or develop and adapt existing technologies to leverage
options that are freely available, eventually creating a green manufacturing process.
Several companies have leveraged natural light for their administration buildings and manufacturing lines. Some have embraced wind energy and quite a few have harnessed solar power. Few more have adopted innovative ideas. Since it is not practically possible to talk to everyone, Auto Components India spoke to a few companies to understand their views on energy conservation and also to share the best practices in their journey towards sustainable manufacturing. Though of paramount importance, energy conservation is certainly not an issue that takes centre stage in our day to day lives. Every one consumes some kind of energy in some form or the other 24×7. It may be noted that December 14th is celebrated as World Energy Conservation day but the order of the day is to observe it all round the year due to depleting fossil fuels and increasing fuel prices, off late owing to unrest in the OPEC countries. Well, what are the options for the manufacturing industry in general and the automotive industry in particular to contain cost of manufacturing? S Ragupathy, Executive Director, Confederation of Indian Industry –Godrej GBC says, fundamentally there are many approaches in containing the cost of manufacturing. Some of the strategies include promoting energy efficiency, adopting Total Cost Management (TCM) practices, improving logistics & supply chain management, and quality management. Highlighting the importance of adopting and promoting energy efficiency and management, he says it is one of the key ways to contain costs and significantly improve the company’s bottom-line. There is immense scope for large number of technological measures to be adopted in the short, medium and long-term to enhance the efficiency of the manufacturing sector.
According to K G Mohan, Deputy Managing Director, Toyota Kirloskar Auto Parts (TKAP), the Toyota group intensively pursues continuous cost reduction. TKAP makes transmission systems for Toyota Kirloskar Motors, and for exports. As a component manufacturer, it faces a huge challenge of increasing costs, besides being exposed to adverse market conditions and foreign exchange fluctuation. The company undertook comprehensive cost reduction activities to partly neutralise these challenges. Company-wide cost reduction targets are systematically distributed along with clear cost ‘Kaizen Plan’ for each division which is followed up meticulously.
Elaborating the concept Mohan articulates that the key focus of cost reduction
activities include plant controllable costs such as energy, tools, defectives, oils, consumables, direct man-hours and logistics. There are cost reduction possibilities at the supplier side through annual price reviews and sharing of best practices. Localisation activity covers not only directly imported items but also extends to raw materials imported by component suppliers in India. Value Analysis / Value Engineering (VA/VE) – as a combined activity with suppliers besides controlling and containing fixed costs and investments.
To achieve lower manufacturing costs, efficiency of operations is a key differentiator, according to the President of Harita Seating Systems Limited, A G Giridharan. The company manufactures a complete range of seats & seat assemblies for automotive and non-automotive applications. “The more efficient one is – efficient in terms of usage of the 4M’s (Materials, Method, Machine and Men) as well as financial resources – the lower will be the cost of manufacturing the product. Customers no longer want to compensate for certain costs. It is a given that these costs are on an increasing trend, but the challenge for the component manufacturer is to see how to put in measures to improve internal efficiencies so that these costs are controlled. We focus on the nature of operations and see how to introduce automation into the process. The manpower deployed in a particular process gives a good indication to this effe ct and we try and see how we can provide low cost solutions to make work easy for people. This will aid in getting output consistently hour after hour,” he says.
The seating system manufacturer is also looking at other elements of conversion like energy, indirect materials, etc. The key is to focus on not just one element but a whole gamut of elements however small or insignificant it may seem, to get the maximum out of a given process. Some of the measures that the company adopts internally include sales per employee, value addition per employee cost, cost of consumables/ Rs Lakh of sale, energy cost/Rs Lakh of sale etc. Ragupathy says housekeeping, fixing leaks and insulation, monitoring & controlling, employee awareness creation & participation and such can save up to 5% with negligible investment. Some of the strategies that a manufacturing unit can adopt and promote are information sharing among stakeholders, promotion of energy conservation culture, monitoring & energy scorecard, implementation of latest & emerging technologies. The need of the hour is to work closely with suppliers and vendors to reduce resource consumption in the supply chain. “Today, many of the auto and auto component manufacturers have started implementing green supply chain initiatives. All these augurs well for the betterment of the economy and ecology. This in turn will make the company globally competitive and in the process become a world class unit,” he states.
Sharing TKAP’s experience Mohan submits that the company pursues all efforts towards making itself an ecofriendly plant through a 3 way approach – Compliance and No complaints, Minimised Environment Risk, and Optimised Environmental Performance. The company became the first industrial unit in Karnataka to get natural gas to run its 6.5mW captive dual fuel power generating plant in February 2013. It is a ‘zero waste discharge’ plant with all sewage being treated on-site and used for secondary purposes like gardening and other utility. Besides, it is a ‘zero land fill waste’ company. “Harita means ‘Greenery’ in Sanskrit; so we are very conscious of ensuring that we are environmentally friendly in our operations,” claims Giridharan. The plant is zero discharge in operations and has a greenbelt in its estate with more than 7,000 trees, turning out to be a rich eco-system for birds and reptiles. It also has rain water harvesting systems in the estate to help in ground water recharging. The company has won several awards for these initiatives including the National Award for Excellence inEnergy Management from CII in 2009,” notes Giridharan.
TKAP, for instance, has reduced the consumption of raw water by creating and installing systems to capture condensate, rain and back-wash water. TKAP along with TKM has released a ‘Green Purchase’ guideline to drive green initiatives amongst their suppliers. In order to reduce resource consumption, the company has reduced consumption of paints and thinners on the final products. There is intensive afforestation of more than 30,000 trees of 31 different species, planted across 12,000 square meters.
Alternative Energy
Today alternative energy sources are no longer prohibitively expensive. Ragupathy says that they are cost effective and sometimes compete with conventional energy sources. For example, power generated by solar photovoltaic sources can compete with diesel based power generators. In fact, in the last 4 to 5 years, the cost of solar photovoltaic has dropped drastically, largely due to the Jawaharlal Nehru National Solar Mission (JNNSM). Auto Electrical major Lucas-TVS use
portable compressors during lean periods to conserve energy. It introduced change of shift timings to avoid evening peak load hours with relative plans to run power intensive machines during night shifts. The company has been getting power from various sources including biomass, solar thermal, solar photovoltaic and wind energy. With this, the green power utilisation has increased from 6% in 2009-10 to 77% in 2013-14 while the dependency on grid power has dropped from 60% to 14% during the same period, said Udayachandran of the company. Irrespective of the production volume, the companymaintains sustained improvement in energy efficiency. The manufacturing process of an automobile involves few operations including machining and painting. While paint shops utilise a significant amount of thermal energy the other operations primarily use electrical energy. The temperature requirement in machine shops is well beyond 300˚C, whereas it is less than 150˚C in paint shops. The paint shop requires water of varying quality and temperature. Generally, hot water at 30–45˚C is required for rinsing the body during pre-treatment. Therefore, solar thermal energy technology may be applied in paint shops for pretreatment, drying and air-conditioning. Solar photovoltaic technology may also be applicable in the press shop, body shop and assembly shops that operate on automated machines powered by electricity, opines Ragupathy.
Giridharan states, “We use T5 energy efficient fittings and LED lights for lighting purposes inside and the periphery of our plant. We also use natural daylight for plant as well as office lighting. Every year we undertake projects to reduce electricity consumed to make ourselves energy efficient. We also use LPG based systems for improving energy efficiency in processes.”
TKAP leverages renewable energy sources mainly focusing on solar energy and applications are in the areas of street lighting, vehicle parking, canteen utensils washing, to run exhausts in toilets and inside shop floor in between machines. The company measures the power consumption per unit in each of its units. Over a period of last 5 years, the average power consumption is measured in kWh/Unit which has been reduced by about 5% per year. For example, in its transmission plant, the average power consumption has come down from 75kWh/unit in 2009-10 to 55kWh/unit in 2013-14. The company has targeted sustained annual reduction of 5% power consumption per unit. “Certain new areas for solar energy application such as converting LPG into vapour are under implementation. Essentially, power cost is one of the key plant controlled cost items which are monitored on daily management,” adds Mohan.
Harita uses solar power at its canteen for cooking purposes. It is currently implementing a project to harness solar energy for process heating inside the plant which would make it eco-friendly. It will be commissioned in 2-3 months time
says Giridharan. “We are also trying to see how we can deploy this to our vendor base as a part of greening the supply chain programme. Having said this, we feel that this is a journey that needs to be carried on rather than focusing on targets for a year or two,” he adds.
Machining
The General Manager (Marketing & Sales), Lakshmi Machine Works, I N Bhattacharya says creating import substitutes of machine tools itself will help conserve cost as the custom duties are high. Currently, about 70% of the machines used by the auto industry are imported, substantially increasing the cost per component. Taking a cue from his own company, he said optimising the spindle and reducing the size of the motor while maintaining the same torque helped customers save about 20% on cost, without compromising on efficiency. With advanced methodologies in castings, material removal is reduced, therefore, the need for robust machines like those in the earlier days, is minimised. This will help contain cost on the capex, operation and real estate since the footprint is minimal. Metrol Corporation India, a company involved in ultra-precision switches for positioning has had its customer experiencing significant savings by introducing probing solution (RCK3 spindle) in the manufacturing process of a meter body component. Their customer was losing about 30 components per day worth Rs 400 each and for 24 working days it was losing about Rs 2.88 lakh per month. With the solution provided by the company the customer could see a return on investment within 28 days, besides, reducing the additional energy used for rework.
Going Green
CII –Godrej GBC in partnership with Shakti Sustainable Energy Foundation (SSEF) conducted a study to highlight energy consumption trends and energy efficiency improvement opportunities of the Indian automobile sector. The major areas with high energy saving potential in automobile plants have been identified to be machining operations, painting, compressed air systems, low thermal mass jigs and fixtures, vapour absorption refrigeration, automation and control, waste heat recovery systems and utilisation of renewable energy sources. Ragupathy is confident that the energy saving potential of this sector will be 15-20%. The Cluster Manager (Marketing – South Asia), Festo Controls, Manoj Dunung says the company that provides automation through pneumatics and electricals takes a holistic view encompassing the compressors, network and distribution, filtration units etc since these are the energy guzzlers. Price should not be the criteria for selection of automation, he says. Instead, the company optimises the solution based on the time period of return on investment. Modular system is the order of the day he feels, adding that flexibility in manufacturing plays a vital role in containing cost of manufacturing. “We give a modular terminal which can be expanded horizontally in terms of pneumatics on one side and electrical I/Os (inputs/outputs) on the other side, as well as vertical functionals such as integrating flow control valve, pressure sensors and such things. Building intelligence is the key,” he affirms. F C Jayakaran, Country Manager, Boge Compressors (India) says energy efficiencies
can be improved in the compressor itself. The air travel distance from suction to discharge can be reduced internally in the compressors as in the case of Boge, which saves up to 35%, resulting in 3% savings in power. Similarly Elgi Equipments Limited’s screw compressors reduce the footprint while also saving energy up to 15%. In addition, it takes half the time for servicing when compared with the older generation compressors, while offering at least twice the life.
Painting
According to the study energy efficiencies can be achieved in painting systems by optimising the volume of air put through the paint booths. Insulation of the drying tunnel can reduce the heat losses through radiation. The radiation losses are estimated to be 5% of the total energy input. About 40 to 60% of the heat input is vented through the exhaust from the painting process, while additional heat is lost as waste heat through the oven walls. Heat can be recovered using heat wheel technology. The largest energy consumer in industrial painting operations is ventilation. A computer controlled system must be utilised to optimise ventilation which is estimated to give a saving of about 5%. Ultra filtration /reverse osmosis for waste water cleaning will further help energy savings.
Welding
In the body weld area, use of computer controls to precisely manage the electric current in welding applications will help conserve energy. Energy can be saved in the weld shop by converting from hydraulic to electric robots or pneumatic to electric servos. In stamping operations, variable voltage controls can be used in drives in order to match speed to load requirements for motor operations, and therefore ensure that motor energy use is optimised to a given application. Replacing pistons on die cushions on stamping presses with air actuators will have close to no air leakages, thus saving energy.
Castings
Casting is a power intensive process consuming more than 55% of the total energy use in foundries. Inefficiencies in melting is generally found in stack losses, inaccuracies in temperature measurement, conduction and radiation losses, poorly fitting charge-well covers and doors, temperature imbalance when adding cold metal to the charge and improper handling procedures. To avoid energy loss in casting operations, the study suggests use of advanced retrofitting technologies which include installing oxygen-enriched fuel combustion, preheating charge material, and recovering heat from flue gases – can improve efficiency in various steps during the melting operation. Also shifting to a stack melter, which is a modified reverberatory furnace that pre-heats the metal charge with waste heat gases. A traditional reverberatory furnace has a thermal efficiency of 20-25% with melt loss of 3-5%, whereas a stack melter has a thermal efficiency of 40 to 50% with a melt loss of approximately 1%. The melting and heat treating operations can be optimised by implementing operating practices and incorporating some cutting-edge melting equipment. Covering the furnace and maintaining refractories will help as it accounts for 10 to 50% of total energy loss depending upon furnace design, operating practices, metals melted, and the source of energy used. Installing radiant panel linings in crucible furnaces which combine a dense, high alumina radiant panel with low thermal-mass insulation back-up materials reduces the heat loss through the sides of the furnace and increases its efficiency.
Udayachandran says, Lucas-TVS has developed alkaline cyanide-free zinc plating process and phased out the hexavalent chromium. Trichloroethane used as degreasing solvent has been replaced by eco-friendly solvent materials. It has installed on-line ambient air quality monitoring system at peripherals to improve the working atmosphere. Besides, the company carries out noise mapping once in 6 months across the factory to identify areas for improvement, he adds.
Heat Treatment
New heat treatment technologies with reduced energy consumption relative to commercial heat treating processes can be adopted. In addition recuperators can be installed to recover waste energy. Temperature sensors to regulate fuel flow in burner, automated dampers to avoid draft losses when burner is in switched off condition, ceramic coatings and replacing inefficient burners in melting and heat treatment will help accrue 10-20 % savings in fuel consumption.
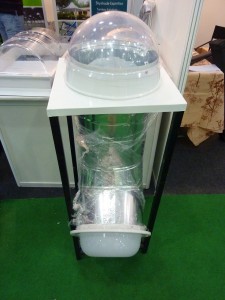
Light Pipes like the one
shown in the photo can provide heat /glare-free daylight for 8-10 hours a day
General Utilities
Establishing formal management structures and systems for managing energy on continuous improvement is an important strategy, states Ragupathy. This is because it helps the plant to manage its energy use and implement energy efficiency measures. Management frameworks, such as ISO 50001, can be used to ensure better organisational management of energy. Certain processes produce waste products that can be incinerated exothermically to provide an ideal fuel for the boiler. The energy saved by using some of these waste streams must be balanced against the potential release of environmental toxins into the atmosphere. Use of other fuels like biomass must also be explored wherever possible.
According to a recent report in a national daily, many hotels in the country have resorted to solar energy to light the garden, pavement and also to preheat water up to 85 degrees and use non-renewable energy sources to boil it. According to rough estimates a 30kW solar power unit can generate about 280kwh of electricity every day for close to 275 days in a year. Quite a few companies have used food waste and waste from the kitchen to produce energy. The degradable waste, when fermented produces methane gas, which can be used for heating purposes through a conventional gas stove.
Right Sizing
Inappropriately sized motors result in unnecessary energy losses. When there is a huge mismatch between the design and operating parameters of the motor, the loading of the motor will be less and efficiency drops. Therefore, by installing a new motor matching the actual requirement, energy can be saved. This correction can save about 1.2% of the eletricity consumption. In addition to downsizing the motors Lucas-TVS has made provision for sleep timers for shop floor lighting and magnetic resonators for DG sets and thermopacs. Replacing standard V-belts with high torque cog-belts will help as they provide about 5-7 % savings in energy. This is because the standard V-belts have drag losses and tend to stretch, slip, bend and compress.
K Sivashanmugam, Senior Business Development Manager, Janatics India says, “Energy can be saved by optimising the pressure of the piston of the pneumatic system, only for the forward or upward movements that are functional. The pressure can be reduced in the opposite direction since the piston is returning back, without any load, to take on the next stroke. This solution has helped a player in the paper industry to save about Rs one lakh on electricity charges per month.” Lighting levels (lumen per surface area) should be set in the design stage for each section of the automobile plant and followed in each step of the ordering, manufacturing and installation stage. Lights can be shut off during non-working hours by non-occupancy sensors. Also, the need for artificial light in buildings can be minimised by efficiently using natural lighting. This can in turn reduce the electrical lighting loads by up to 70%. For instance, advanced day lighting systems like the one manufactured by Skyshade offers over 50% energy savings; using ‘light pipe’ that collects sunlight and conducts it through pipes to diffuse the system. This unit provides heat and glare free daylight for 8 to 10 hours a day. As part of its continuous improvement in going green, Lucas-TVS has become a paper-free company. Interestingly, it is one of the few companies to achieve paperless documentation, the system to save trees. In the current fiscal the company plans to effectively handle the waste coolant recycling system. Besides, it also plans to utilise canteen food waste for bio-gas generation.
CII with the support of all the stakeholders has launched GreenCo Rating System, the first of its kind in the world. GreenCo Rating is a holistic mechanism for evaluating the performance of companies on the ecological front. It rates companies on the environmental friendliness of their activities and provides leadership and guidance on how to make products, services and operations greener. GreenCo helps drive excellence in resource conservation, bottom-line improvement, green corporate image and goes much beyond compliance. It also helps provide strategies for longterm competitiveness, besides being an excellent tool for top management to monitor their Green Performance. As of now over 25 companies are Greenco rated, and over 75 companies are working on this rating system. Some of the companies in the automobile segment going the Greenco way include Tata Motors, Sundaram Fasteners, Brakes India, and JK Tyre & Industries Limited. The GreenCo rating system is expected to play a catalytic role in greening Indian industry, paving the way for the country to become one of the global leaders in green business by 2022. Energy conservation is everybody’s business, be it anywhere. Unless there is a conscious decision taken by every individual and practised continuously, the results cannot be achieved. ACI
extreme dieting and constipation
Much of the is dependent upon the foods on your table, when you
are eating them as well as the amount and type of exercise you are doing.
Dieting is about breaking habits and learning a new one, which
doesn’t come naturally at all. This is the reason it usually
is better for the blood sugar levels level, as well
as your health generally speaking, to nibble on sensibly and well instead of starving
yourself.