VE Commercial Vehicles is banking on integration for BSVI compliance to match Volvo Groups’ global success in India.
Story by: Bhushan Mhapralkar
VE Commercial Vehicles (VECV) is banking on system integration as an Original Equipment Manufacturer (OEM). Capitalising on the capabilities of the sister concern VE Powertrain (VEPT) plant to deliver its BSVI product range, the company has long announced that it is BSVI ready. The feat was attained with the BSVI module integration from the sister concern VEPT plant commissioned in July 2013 at Pithampur, in Madhya Pradesh. With a current capacity of manufacturing 75,000 units of the five and eight-litre engines, the latter is reckoned as the hub for meeting the medium-duty automotive engine requirements of Volvo Group globally, including at VECV. An estimated 1,20,000 Euro6 base engines have been manufactured at the plant with claims of the engine technology tested for over 5.6 million kilometres. The plant mirrors the Volvo Powertrain assembly plant in Sweden with its ability to manufacture Euro6 engine units. It is noteworthy that the base engines for Euro6 requirement of the Volvo Group are being supplied to their Venissieux plant, in France. The platform on adaption doubles up as the Euro3 to Euro5 engines requirements of the company globally.
Leveraging the knowledge repository built as an outcome of supplying Euro6 engines to Volvo Groups’ Venissieux plant, in France, VECV has tweaked these engines to suit the Indian duty cycles. Averred Vinod Aggarwal, Managing Director and Chief Executive Officer, VECV, “We have an experience of over six years in manufacturing EuroVI engines and a knowledge repository of data gathered from across Volvo engines used in 1,20,000 thousand trucks worldwide. All that experience and nuances in engines will be incorporated in the driveline, so we are prepared to deal with complexity.” Aggarwal explained that in contrast to the duty cycles of a Euro6 truck, the BSVI trucks had to be built to align with Indian duty cycles, regulatory requirements and a lower power-to-weight ratio. With a mechanism in place to identify and feed the right set of piston rings for the assembly of the piston in an engine, the VEPT facility has in place advanced process measurement equipment and setup for critical operations. If the deployment of SPMs with work changer points at a high level of automation, the Pithampur facility is clearly about getting it right the first time around. Having in-process verification and multiple tests, the plant is a reflection of how the initial reservations about the viability of producing global-spec engines in India were successfully overcome. Deploying AGVs for final assembly, the frugal engineering approach at VEPT is based on the custom proto build.
Advanced capability
Comprising of a hybrid concept with wireless charging, equipped with safety features recommended by EU standards, the facility has in-process verification at every stage. With regular forums being held to share knowledge and improve productivity by addressing areas of concern, the VEPT facility has, and continues to play a key role in VECV’s quest for BSVI. Consider, for example, the innovations in the BSVI cylinder head sub-assembly where the injectors are assembled and the engine proceeds for a leak test. Conventionally, engine manufacturers conduct the leak test either when the engine is entirely ready or when the fuel flow is higher and efficiency, not the most optimum. Here, the leak test is conducted when the injector is fitted on to the engine. Any anomaly in fuel flow addressed at this stage, and with the engine assembling process in progress, the VEPT engine plant has achieved a good balance between the processes and cycle time. Unique is the smart cell for cylinder head assembly.

An in-process verification module ensures that digital verification technology operator activity and errors are nullified on the go.
Smart approach
The entire valvetrain unit is assembled on to a machine called Smart Self, which can assemble 168 parts in 120 seconds and is a first-of-its-kind doing duty in an Indian manufacturing unit. The VEPT facility has a system enabled (pull-based) minimum material movement. An amount of customisation is apparent given the combination of automation and manual work. If machines like the Smart Self depict how customisation and automation have led to the optimal use of manpower, the VEPT facility is about keeping costs in check without losing sight of quality and cycle time. Interestingly, there is an automatic process to set the valve clearances. The engines that roll out of the facility are well-configured thus. This is expected to prove to be of much help in the BSVI environment. The low tolerances leading to less noise, especially in an environment where BSVI norms prescribe stringent NVH levels, the engines rolling out of Pithampur are indeed well-configured. With the quality adherence measures integrated within different processes, the quality assurance department takes care of product certifications. Quality inspectors form a part of the production team, thereby negating the need to have additional personnel for this task.
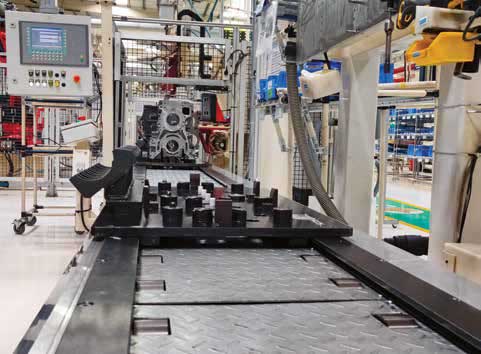
VEPT has implemented frugal management techniques, which improve manpower productivity and reduce downtime.
World-class manufacturing
Implementing the World Class Manufacturing (WCM) practices from Volvo’s global operations at the Pithampur plant, the company, to provide an ergonomic advantage to the operator has engineered the engine assembly process such that it is done with the engine kept vertically aligned. This is contrary to the common practice of the engine being positioned horizontally. VEPT and VECV have been working closely together. With the BSVI development consisting of much R&D, testing and validation, the two entities have been leveraging their proximity to the Volvo Group to gather knowledge and to anticipate as well as tackle any disruptions that may come their way. Among other salient features of the plant is the machining cylinder block of four and six-cylinder engines, in-process measurement of critical operations, verifications and multiple tests, SPMs with work changer to minimise part change time in machining, system enabled (pull-based) minimum material movement and repacking under a controlled environment. VECV unveiled the first BSVI vehicle in June 2019 with the introduction of new-generation Pro2000 series. As per company claims, deliveries of BSVI vehicles have commenced in select markets and the entire new range of trucks and buses will be made available throughout the country ahead of the April 01, 2020 deadline.
Higher Uptime
At VE Commercial Vehicles, a newly set up Uptime Centre spread over an area of 2400 sq.ft will be the backbone of its BSVI range of commercial vehicles. A vital cog in the wheel of the adapting Euro6 Technology (deemed as Eutech6) to Bharat Stage VI emission norms, the centre to be optimised in a phase-wise manner boasts of 87 employees who will offer 24×7 support facility helmed by specialists in the field. To bolster its effectiveness of the new centre, VECV has deployed a GPS enabled service van available on call. Through remote diagnostics, the company will offer quick repair of BSVI vehicles. Within a time span of four hours, a diagnostic learning document is created for the dealership to help customers attain a higher uptime. Under vendor support services, claimed to be a unique initiative, the company is collaborating with company vendors to offer service within 24 hours. This includes information on parts availability and quantity to VECV customers. In case of part unavailability at the dealership, the part will be reached to the particular dealer. Failing which the company banks on the regional three distribution centres. A failure at this level will trigger the identification of the part from the HQ office (mother warehouse) at Pithampur and shipped thereafter with a TAT of 24 hours. VECV aims to offer predictive diagnostics (in phase 2) and specialised field support to all BSVI VECV vehicles. The ‘Uptime Enablement’ of all workshops in the network is claimed to be progressing rapidly to ensure the availability and adequacy of people, process and infrastructure.
–Deven Lad
Leave a Reply