Text: Anusha B
Machining industry plays a vital role in all industries especially the automobile sector. Tool making, die making and component manufacturing is formed with the help of machining industry. Germany is known for its innovations and machining industry never goes untouched by them. As and when auto industries steps into the next phase, the supporting industries is also expected to transform to the next level. In order to highlight the latest machining technologies, German Machine Tool Builder’s Association (VDM) and Indo-German Chamber of Commerce (IGCC) organised a symposium on ‘Innovations in Production Technology – Machine Tools from Germany’ in Chennai recently. The 1-day event discussed the latest trends in the machining industry and more that 17 companies highlighted their innovations.
Kapp Gruppe GmbH, the company which manufactures profile grinding and generating grinding for finishing of gears and profiles came up with some innovative solutions. Matthias Heinemann, representing the company said, “We are here in India for more than 25 years. No doubt, the country is developing but still infrastructure and power are picking up in a turtle pace. We are the manufacturers of profile grinding machines and customised the same with respect to the requirements of manufactureres. These machines are used for manufacturing gears and shafts of different sizes ranging from 100-500mm. Our products can take care of complex geometrical requirements too as auto industry comes up with new requirements at a shorter time and obsolete the prevailing standards with new perspectives on par with customer’s taste and governing body’s revised formulations. Dressing tools and grinding tools are also manufactured in-house and because of this we are able to achieve soft finishing of gears and profiles. More than 50 years we serve the market with grinding tool solutions and mass production in automobiles too is taken care.”
Commenting on the innovative solutions for steering systems, Klaus Thausner from Leistritz GmbH said, “Since 111 years we are responsible for steering system solutions for auto industries. For more than 4 decades, we develop machine tools for auto industries from mass production to single piece production. We provide turbine technology solutions, pump technology solutions, extrusion technology solutions and production technology solutions. Pertaining to auto industries we have a electric power aided innovation for steering system EPS (Electric Power aided Steering System) solutions, which we provide for premium car manufacturers. We supply whirling machines, rolling machines and key seating machines. Whirling machines are used for cutting operations, where the life of the tool goes up and the heat generation is also less even during high speed cutting. Therefore we eliminate coolant and the production time is also reduced. With our findings, the number of processes got reduced for pinion and rack steering technology, and high accuracy level is achieved.”
MAG IAS, the machine builder for manufacturing engine components highlighted its innovations and talked about the auto industries. Voicing on the occasion, the company’s spokesperson Dr Manfred Berger said, “We provide turn-key solutions and pertaining to auto industries we give engine component solutions. We have our own spindle which has long life. India is growing in auto industries but not in the pace we expected. China slows down but still growing and Europe is a dynamic market. Every 5 years drastic changes happen in every industry and auto industry could not be left behind. We have to be solution-ready and product-ready every time to parallel ourselves with the growing trends. Hence we are able to be an innovation leader in the market across world. We should have product flexibility, volume flexibility, process flexibility and system efficiency. Hitherto whatever we have installed and invested 30-35% has become obsolete and Euro spent for the same is trashed. Only 10-15% is getting utilised for the emerging market. For an instance, the spindle should be able to run long time in the emerging trends. The process steps are squeezed to 5 steps and to point out adapter plate solutions also add in our innovation lines of engine components. Downsising of engines performs well in the market and we have coded temperature optimisation solutions for the same which in-turn contributes to fuel economy and emission statistics. Engine will be 80 degrees warm all the time when we have all these solutions solved in the engines.”
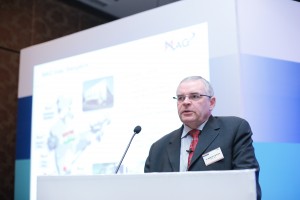
Dr Manfred Berger of MAG IAS gave an insight on new technologies for volume production of engine components
DMG MORI, a German-Japan collaboration company highlighted its machining solutions and its multi tasking capabilties. Addressing on the occasion, S Ravishankar, Managing Director of Indian operations pointed that, “We have more than 300 products and we master in turning, milling, eco clean, ultrasonic/lasertec, ecoline and automotive electronics service. We have eccentric machining solutions and to highlight, no special machines are required for addressing any tooling needs as our standard machines are equipped with all special machine fits necessary.”
Representing Gleason-Pfauter GmbH, Heiko Meier addressed the solutions they have in hand for total gear solutions. Meier asserted, “Through power skiving process we have total gear solutions. We focus on gear cutting, hobbing, grinding, shaping and everything a gear expects is delivered by us. Gear cutting speed is excellent with our machines. Shaping of gears is an advantage and through this process we could output ring gears in 6 cuts with correct profile and the customised measurement. Our process is 6 times faster compared to shaping and the quality is equal or better than shaping. Surface quality is high and tool cost is same but cost per part is significantly low. Always final price rules the margin of the customers and 1 power skiving machine against 4 shaping machines is the ratio and the production time also clocks low. In skiving machines, cycle time is less than 20 minutes against 100 minutes and productivity is 2-3 times faster compared to shaping machines.”
Andre Kind representing SAMAG GmbH, which is specialised in machine tools, automotive parts and truck components focuses more on thermally stable, vibration proof machines. Kind explained that, “Our machines are used for heavy cutting applications in tooling industry. We have state-of-the art solutions for clamping for camshafts, gearshafts, engine valves and also manufacture special purpose machines. We are providing innovations in machining of parts and components in powertrain. Downsising impacts us too a lot and we are driven by lightweighting options.”
Maximilian Waizenegger from Hermle AG compared the advantages of 5-axis machines juxtaposing 3-axis machines. He glimpsed, “We have parts sourced from Germany. We have done service for more than 10 years and to highlight, the products made out of our machines have high accuracy in surface finish. Downsising leads to increased pressure and casting would be a major hiccup and if that is the case how do we go for cutting process? And how could we achieve surface finishing? The best concept of all these is 5-axis machines and this acts as a benchmark. The benefits of the machine are, it could achieve complex shapes and cutting edge and cycle time performances are outstanding when juxtaposed with 3-axis machines.”
With 20 years of vertical turning machine manufacturing experience, EMAG Group highlighted their vertical turning concept plus deep integrated automation. Andreas Zieger, who represented the group said, “We carry with us immense knowledge in the industry. Indubitably, 5-axis machine is a good solution but cycle time is high. Speed is high with our machines and our machines are available at an economic cost. Life-time of the machine is also high. The foot print of our machines is very low and this is achieved because of the integration of lot of technologies in the machines. We still work more to have all the concepts coded in one machine. We are going for Laser welding to output light weight products. The concept we derive is modular which is interlinking of technologies and we partner with companies to derive the best integration.”
A N Chandramouli who represented Heckert GmbH said, “V-engines are very good to have and we have 5-axis machine solutions for V-engines. We could make complex parts and the processing time is less and accuracy is more. We have achieved integration in the process of drilling, mining and turning.” All together the event marked an epoch in the industry and with innovations, the industry will taste the ladders of success. ACI
Leave a Reply